The bag-in-box system, a staple in liquid packaging, offers efficiency and extended shelf life. Understanding its manufacturing process provides valuable insights into its reliability. This blog post delves into creating these versatile packaging solutions step by step.
We’ll explore the materials, machinery, and quality control measures involved in bag-in-box production. Each stage is crucial for ensuring a product that meets industry standards and consumer expectations, from selecting high-barrier films to the final assembly and testing.
What Is Bag-in-Box
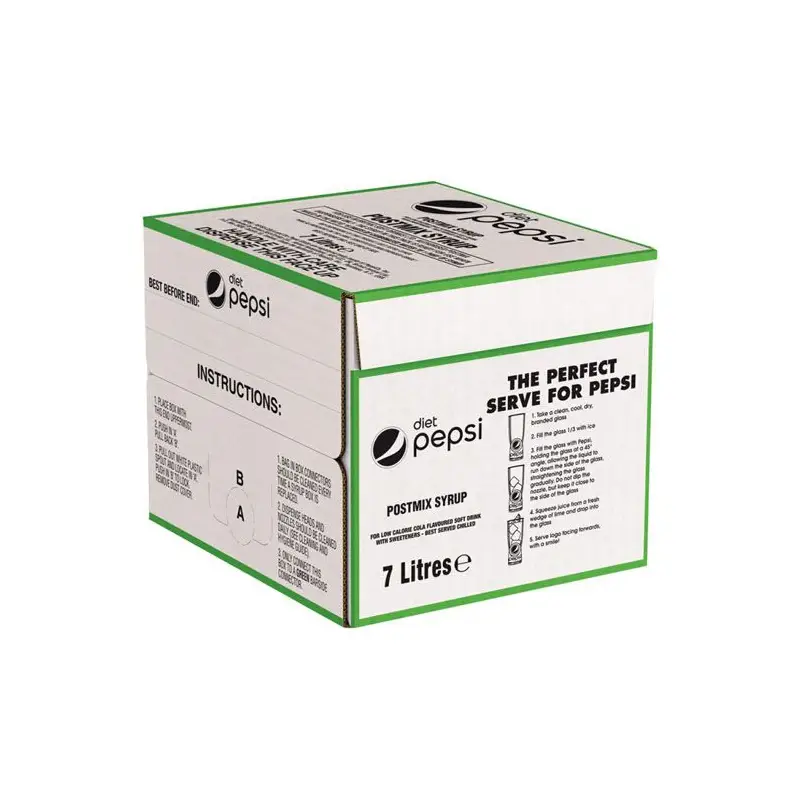
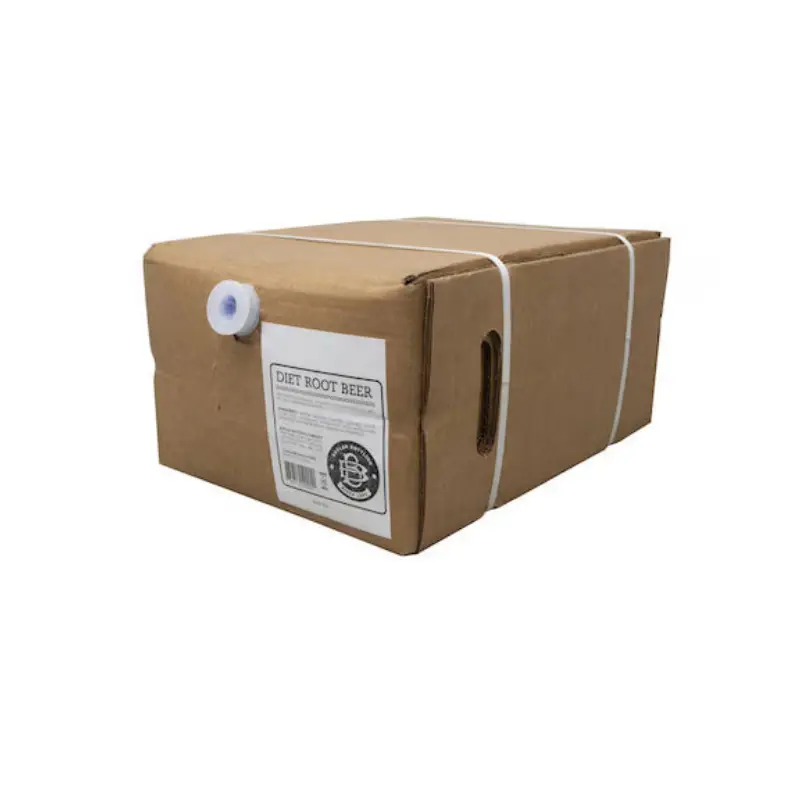
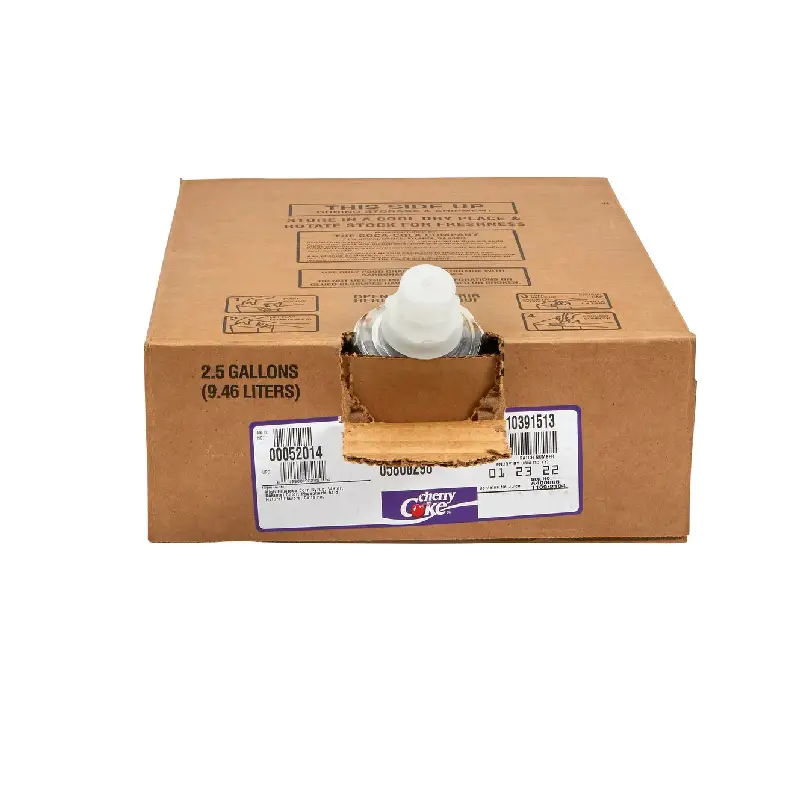
Bag-in-box (BIB) is a packaging system designed for the storage and dispensing of liquids and semi-liquids. It consists of a flexible, multi-layered plastic bag that is housed within a corrugated cardboard box. This combination provides a robust and efficient way to protect and distribute various products, minimizing exposure to air and contaminants.
The system is engineered to extend product shelf life by preventing oxidation and maintaining freshness. It typically includes a dispensing tap or valve, which allows for controlled and convenient pouring. This design is widely used across industries, from beverages and syrups to cleaning solutions and liquid foods, offering a space-saving and cost-effective alternative to traditional rigid containers.
How to Make Bag-in-Box
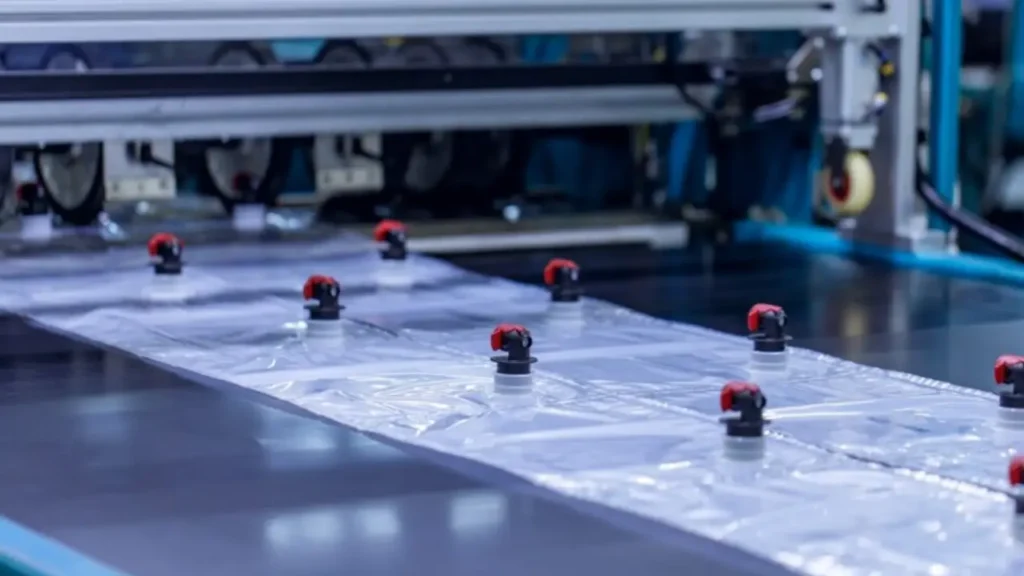
Crafting a bag-in-box system demands meticulous attention to detail and precision engineering. We understand that each step is crucial in delivering reliable and high-quality packaging solutions. From selecting the finest materials to the final assembly, our process ensures product integrity and efficient dispensing.
Let’s explore the intricate journey of how we create bag-in-box systems, step by step.
Step 1: Material Selection – The Foundation of Quality
Recommended Bag-in-Box
We begin by meticulously selecting the raw plastic resins that will form the multi-layered film. This stage is critical, as the material’s properties directly impact the final product’s performance. We consider factors like barrier resistance against oxygen, moisture, and light, as well as the material’s flexibility and compatibility with the intended liquid.
We source resins from trusted suppliers who adhere to strict quality standards, ensuring consistency and reliability. We prioritize food-grade materials for applications in the food and beverage industry, guaranteeing safety and compliance. We also assess environmental impact, favoring recyclable or biodegradable options where possible.
Step 2: Film Extrusion – Crafting the Protective Barrier
Next, we melt and extrude the selected resins through a sophisticated die, creating a continuous sheet of multi-layered film. This process demands precise temperature and pressure control to ensure uniform film thickness and consistent quality across the entire roll. Each layer within the film is designed for a specific purpose.
For instance, an inner layer might provide chemical resistance, while an outer layer offers structural integrity. We utilize advanced co-extrusion technology to bond these layers seamlessly, eliminating the need for adhesives that could compromise product safety. This multi-layered film is the heart of the bag-in-box system, providing a robust barrier against external contaminants and preserving the product’s freshness.
Step 3: Bag-in-Box Formation – Shaping the Inner Vessel
We then feed the extruded film into high-speed bag-making machines, where it’s precisely cut and shaped into the desired bag size. Automated machinery ensures consistent dimensions and accurate cuts, minimizing waste and maximizing efficiency.
We employ advanced cutting and folding techniques to create bags that fit perfectly within the outer box, optimizing space utilization and reducing material costs. The bag’s design is tailored to the specific product, considering factors like volume, viscosity, and dispensing requirements. We also incorporate features like gussets or folds to enhance the bag’s structural integrity and prevent leaks.
Step 4: Bag Sealing – Ensuring Leak-Proof Integrity
Following bag formation, we employ advanced heat-sealing techniques to create robust and secure seals. This step is crucial for preventing leaks and maintaining product integrity during storage and transport. We utilize automated sealing machines that apply precise temperature and pressure, ensuring consistent seal quality across all bags.
Each seal undergoes rigorous testing to verify its strength and leak-proof performance. We also consider the seal’s compatibility with the product, ensuring it won’t degrade or contaminate the contents. We meticulously inspect each bag to ensure it meets our stringent standards, guaranteeing reliable packaging.
Step 5: Fitment Application – Facilitating Efficient Dispensing
We then attach fitments, such as taps, valves, and spouts, to the formed bags, tailoring the choice to the product’s viscosity and dispensing needs. These bag-in-box fitments are securely bonded through heat sealing or mechanical methods, ensuring a reliable and leak-proof connection. Automated equipment precisely positions and attaches the fitments, guaranteeing consistency and accuracy.
We perform quality checks to verify the fitment’s functionality, including flow rate, drip prevention, and ease of use. We also ensure the fitment’s material is compatible with the product, preventing any chemical reactions or contamination.
Step 6: Bag-in-Box Manufacturing – Constructing the Protective Shell
Simultaneously, we manufacture the corrugated cardboard boxes that provide structural support and protection for the inner bags. These boxes are cut, folded, and glued to meet the required dimensions, ensuring a snug fit and preventing damage during transport.
We use high-quality materials and precise manufacturing techniques to create robust and durable boxes. We also consider the box’s design, incorporating features like handles, tear-away panels, and dispensing windows to enhance user convenience. The box’s printing and labeling are also critical, providing branding and product information to consumers.
Step 7: Bag-in-Box Insertion – Combining Components for Optimal Performance
We carefully insert the formed bags, with attached fitments, into the corrugated cardboard boxes. Automated machinery ensures precise positioning and a secure fit, preventing damage during transport.
We conduct visual inspections to ensure the bags are correctly placed and the fitments are properly aligned. This step is critical for maintaining product integrity and preventing leaks. We also verify that the box’s design and dimensions are compatible with the bag, ensuring a seamless and functional packaging system.
Step 8: Final Assembly and Packaging – Delivering Quality to Our Customers
Finally, we seal and label the boxes, completing the final assembly process. We conduct comprehensive quality control checks to ensure the assembled bag-in-box units meet all specifications, including leak-proof performance, dispensing functionality, and aesthetic appeal.
The units are then palletized and prepared for distribution, ensuring they are ready for safe and efficient transport. We ensure that each assembled unit is ready for market, maintaining our commitment to quality and reliability. We also consider the environmental impact of our packaging, favoring recyclable or biodegradable materials and minimizing waste.
Conclusion
In summary, the bag-in-box manufacturing process involves meticulous steps from material selection to final assembly, ensuring product integrity and efficiency. Understanding each stage highlights the complexity and precision required. This process is crucial for delivering high-quality, reliable packaging solutions.
The integration of advanced technologies and quality control measures guarantees consistent product performance. From film extrusion to fitment application, each phase contributes to the overall functionality and durability of the bag-in-box system. This results in packaging that protects and preserves a wide range of liquids.
Ready to enhance your product packaging with premium bag-in-box solutions? Partner with BN Pack for wholesale options tailored to your needs. We offer customizable, high-quality packaging designed for optimal product protection and dispensing. Contact us today to explore our range and streamline your packaging process.