Polylactic Acid (PLA) packaging is rapidly gaining traction as a sustainable alternative to traditional plastics. Derived from renewable resources like corn starch or sugarcane, PLA offers a biodegradable and compostable solution, addressing growing environmental concerns. This guide explores the diverse applications and benefits of PLA in the packaging industry.
We’ll delve into the manufacturing process, properties, and various uses of PLA packaging, highlighting its environmental advantages and potential drawbacks. Whether you’re a business seeking eco-friendly packaging or a consumer curious about sustainable options, this comprehensive guide will provide valuable insights into the world of PLA.
What Is Polylactic Acid
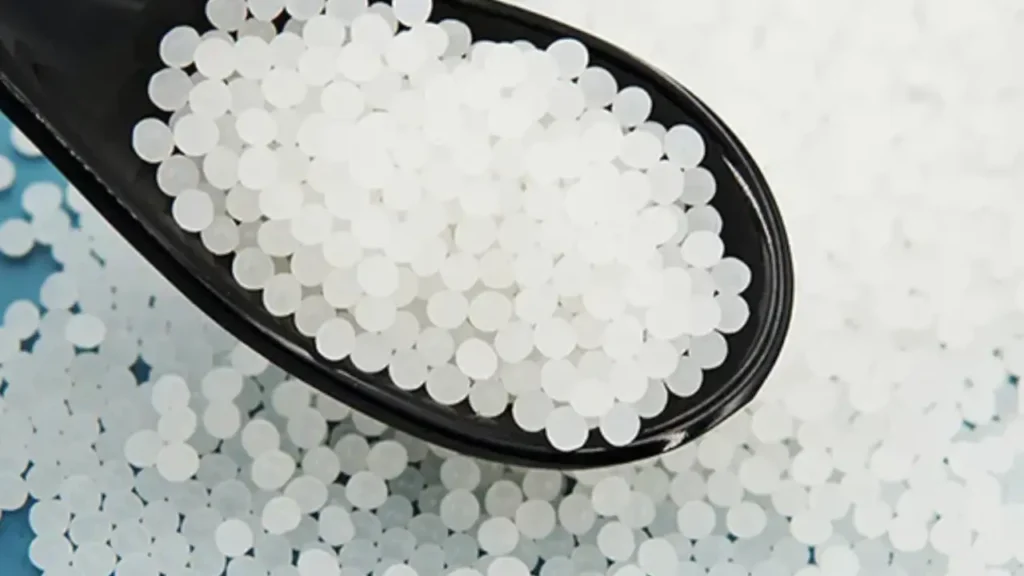
Polylactic acid (PLA) is a bioplastic derived from renewable resources, such as corn starch, sugarcane, or cassava. Unlike traditional plastics made from petroleum, PLA is biodegradable and compostable under specific conditions. This makes it a more environmentally friendly alternative, reducing reliance on fossil fuels and minimizing plastic waste.
What Is Polylactic Acid Made of
Polylactic acid (PLA) is primarily made from renewable resources, specifically plant-based sugars. The most common source is corn starch, but it can also be derived from:
- Sugarcane
- Cassava roots
- Potato starch
- Beet pulp
The process begins with fermenting these sugars, similar to how yogurt is made. This fermentation converts the sugars into lactic acid, which is then polymerized to create polylactic acid. This polymerization process links the lactic acid molecules together, forming long chains that give PLA its plastic-like properties. This plant based origin is what allows it to be compostable.
Polylactic Acid Melting Point
The melting point of polylactic acid (PLA) is a critical factor influencing its suitability for packaging applications. Typically, PLA has a melting point range of approximately 130-180°C (266-356°F), which is relatively low compared to traditional petroleum-based plastics. This lower melting point has both advantages and disadvantages for PLA packaging.
One significant effect is PLA’s sensitivity to heat. Packaging made from PLA is generally not suitable for high-temperature applications. For instance, it’s not ideal for packaging hot liquids or foods that require heating in a conventional oven. Exposure to elevated temperatures can cause PLA packaging to deform, soften, or even melt, compromising its structural integrity and the product it contains. This limits its use in applications where heat resistance is crucial, such as microwaveable containers or hot-fill packaging.
However, the lower melting point also offers advantages during the manufacturing process. It requires less energy to process PLA compared to plastics with higher melting points, contributing to a lower carbon footprint during production.
What’s more, it allows for easier processing techniques like thermoforming and injection molding, which are commonly used in packaging manufacturing. The lower melting point also facilitates easier sealing, which is important for creating airtight packaging to preserve food freshness. In essence, while the lower melting point limits PLA’s use in high-temperature environments, it simplifies manufacturing and reduces energy consumption, making it a viable option for many ambient and chilled packaging applications.
Polylactic Acid Uses
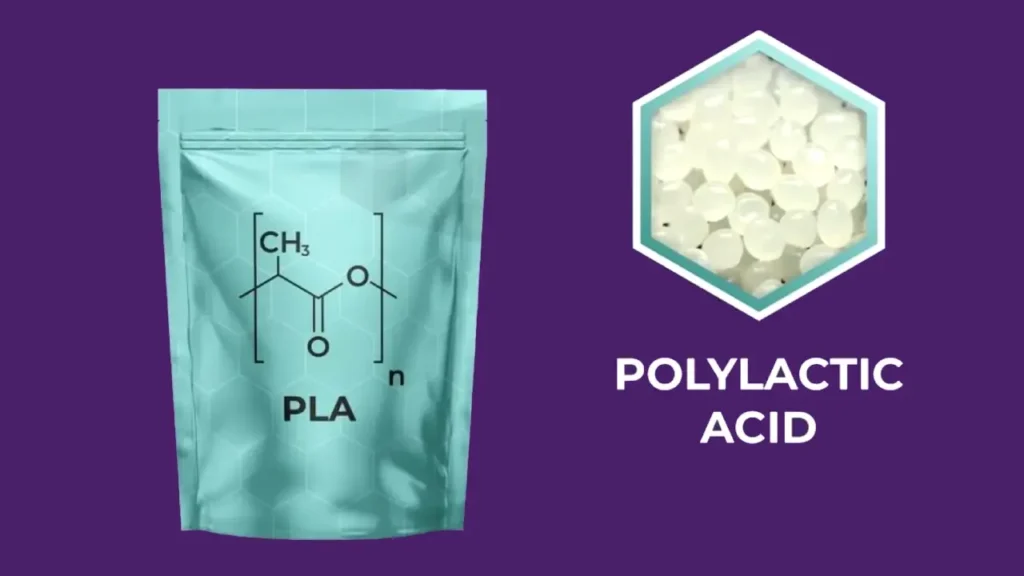
Polylactic acid (PLA) finds a wide range of applications due to its biodegradability and versatility. Primarily, it excels in packaging, particularly for food and beverage items. Its ability to be formed into films, containers, and bottles makes it a popular choice for single-use packaging. The growing demand for sustainable alternatives has propelled PLA into mainstream packaging, replacing traditional plastics in many consumer goods.
Beyond packaging, PLA is increasingly used in:
- Medical Applications: Due to its biocompatibility, PLA is used in sutures, implants, and drug delivery systems. Its ability to degrade naturally within the body makes it ideal for these applications.
- 3D Printing: PLA is a common filament for fused deposition modeling (FDM) 3D printers. Its low melting point and ease of use make it a popular choice for hobbyists and professionals alike.
- Textiles: PLA fibers can be spun into fabrics for clothing and other textile products. This offers a more sustainable alternative to synthetic fibers derived from petroleum.
The environmental benefits of PLA are a major driver of its increasing adoption. As consumers and businesses become more conscious of their environmental impact, PLA offers a viable solution for reducing plastic waste. However, proper composting facilities are essential for PLA to fully degrade, highlighting the need for improved infrastructure to support its widespread use.
Polylactic Acid Synthesis Properties and Applications
Polylactic acid (PLA) synthesis begins with the fermentation of sugars derived from renewable resources like corn starch or sugarcane. This fermentation produces lactic acid, which is then polymerized, either through direct condensation or ring-opening polymerization of lactide, into PLA.
The resulting polymer’s properties, such as molecular weight and crystallinity, can be tailored during synthesis to meet specific application requirements. This flexibility makes PLA a versatile material for various industries.
PLA exhibits several desirable properties, including:
- Biodegradability: Under controlled composting conditions, PLA breaks down into carbon dioxide, water, and biomass.
- Biocompatibility: It is non-toxic and can be used in medical applications.
- Thermoplasticity: PLA can be melted and reformed, allowing for various processing techniques like extrusion and injection molding.
- Relatively High Strength and Stiffness: Suitable for many packaging and structural applications.
These properties make PLA suitable for diverse applications. In packaging, it’s used for food containers, films, and bottles. In the medical field, it’s employed in sutures, implants, and drug delivery systems. Additionally, PLA is a popular material for 3D printing filaments, and it’s also finding uses in textiles and consumer electronics. The increasing demand for sustainable materials is driving further research and development in PLA synthesis and applications.
Polylactic Acid for Packaging
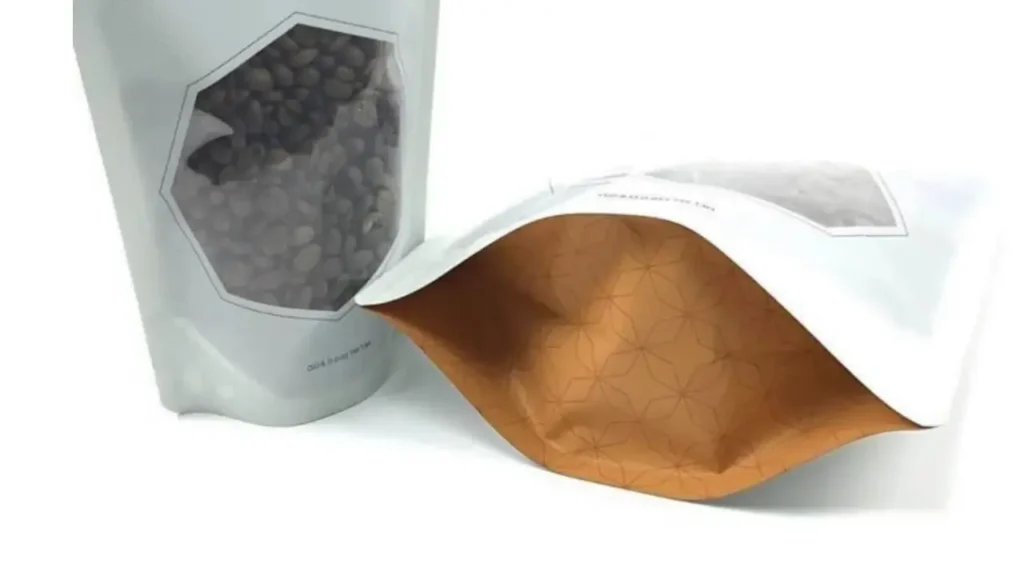
Polylactic acid (PLA) is rapidly gaining traction in packaging due to its biodegradability and renewability, offering a sustainable alternative to traditional plastics. Its versatility allows it to be processed into various forms suitable for diverse packaging needs, from rigid containers to flexible films. The growing consumer demand for eco-friendly solutions has propelled PLA into a leading role in the development of sustainable packaging materials.
Specific applications of PLA in packaging include:
- Polylactic acid tea bags: Providing a compostable alternative to traditional nylon or paper tea bags.
- Polylactic acid coffee bags: Used for single-serve coffee pouches and larger bulk coffee packaging.
- Food containers: PLA is used for disposable plates, cups, and takeout containers, reducing reliance on petroleum-based plastics.
- Produce packaging: PLA films and clamshells are used for packaging fruits and vegetables, extending shelf life while remaining compostable.
- Blister packs: Used in pharmaceutical and consumer goods packaging, offering a biodegradable alternative to traditional blister packs.
- Shrink wrap: PLA can be processed into shrink wrap films for bundling and packaging products.
The various types of PLA packaging cater to different industries and applications. Its ability to degrade under composting conditions makes it an attractive option for businesses looking to reduce their environmental impact. As technology advances, PLA’s performance and cost-effectiveness are expected to improve, further expanding its use in the packaging sector.
Polylactic Acid Advantages
Polylactic acid (PLA) packaging offers several key advantages, primarily centered around its environmental sustainability. As a bio-based material, PLA is derived from renewable resources, reducing dependence on fossil fuels. This leads to a lower carbon footprint compared to traditional plastics.
PLA is compostable under industrial conditions, meaning it can break down into natural elements, minimizing long-term waste.
Specifically, PLA packaging offers:
- Reduced Environmental Impact: Lower greenhouse gas emissions and less reliance on finite fossil resources.
- Compostability: Breaks down in industrial composting facilities, reducing landfill waste.
- Renewable Resource Origin: Made from plant-based materials, supporting sustainable agriculture.
- Versatility: Can be used for various packaging formats like films, containers, and bags.
- Consumer Appeal: Aligns with growing consumer demand for eco-friendly packaging.
How is Polylactic Acid Packaging Made
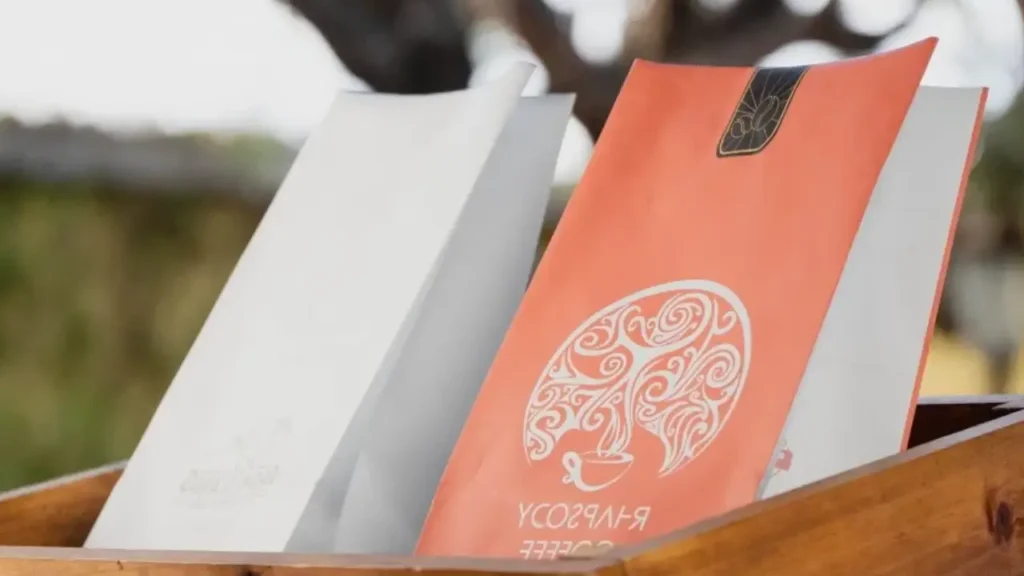
The polylactic acid (PLA) packaging manufacturing process transforms raw PLA resin into functional packaging solutions. Here are the key steps to manufacture PLA packaging in our packaging factory production line.
Step 1: Resin Preparation
The process begins with PLA resin pellets, which are typically derived from fermented plant sugars. These pellets are often blended with additives, such as plasticizers, stabilizers, or colorants, to tailor the properties of the final packaging. These additives enhance flexibility, heat resistance, or visual appeal. The prepared resin is then dried to remove any moisture, which can affect the processing and quality of the packaging.
This stage is crucial for ensuring the consistency and performance of the PLA packaging. The precise formulation of the resin blend is determined by the specific requirements of the intended application. Careful control of the mixing and drying processes is essential to achieve uniform quality and prevent defects in the final product.
Step 2: Processing and Forming
The prepared PLA resin is then processed using various techniques, depending on the desired packaging format. Common methods include:
- Extrusion: For producing films, sheets, and thermoforming stock. The molten PLA is forced through a die to create a continuous profile.
- Injection Molding: For producing rigid containers and molded parts. Molten PLA is injected into a mold cavity, where it solidifies.
- Thermoforming: For producing trays, cups, and clamshells. PLA sheets are heated and formed over a mold using vacuum or pressure.
- Blow Molding: For producing bottles and containers. Molten PLA is extruded into a parison, which is then inflated inside a mold.
Each processing method involves precise control of temperature, pressure, and speed to ensure consistent quality and dimensional accuracy. The formed PLA packaging is then cooled and trimmed to remove any excess material.
Step 3: Finishing and Packaging
After forming, the PLA packaging may undergo finishing processes, such as printing, labeling, or surface treatments, to enhance its functionality or aesthetics. Printing allows for branding and product information to be added, while surface treatments can improve barrier properties or provide a specific texture.
The finished packaging is then inspected for quality control to ensure it meets specifications. Finally, the PLA packaging is packed and prepared for distribution. Proper packaging is essential for protecting the product during transport and storage. The final product is then ready to be shipped to end-users.
Is Polylactic Acid Biodegradable
Yes, polylactic acid (PLA) is biodegradable, but it’s important to understand the specific conditions required for it to break down. PLA is derived from renewable resources like corn starch or sugarcane, making it inherently different from traditional petroleum-based plastics. Its biodegradability means that under the right conditions, microorganisms can consume PLA, converting it into carbon dioxide, water, and biomass.
However, PLA’s biodegradability is not as straightforward as some might believe. It typically requires industrial composting facilities with controlled temperature and humidity levels to break down effectively. In home composting environments, PLA may take significantly longer or not degrade at all. Therefore, while PLA is a more sustainable option than traditional plastics, its end-of-life management is crucial for realizing its environmental benefits.
Conclusion
PLA packaging presents a sustainable and versatile solution, offering a reduced environmental footprint compared to traditional plastics. Its biodegradability and compostability make it ideal for eco-conscious brands. Understanding its properties and applications allows businesses to leverage PLA effectively, meeting consumer demand for greener alternatives.
From food packaging to retail goods, PLA’s adaptability shines. Careful consideration of its limitations, such as temperature sensitivity, ensures optimal performance. As technology advances, PLA’s role in sustainable packaging will continue to expand, driving innovation and reducing plastic waste.
Ready to transition to eco-friendly packaging? Contact BN Pack today for wholesale PLA packaging solutions. We offer a wide range of customizable options to meet your specific needs and contribute to a more sustainable future.