This blog post will delve deeper into the frequently asked question: how much do biodegradable bags actually cost? We’ll not only explore the factors influencing their price but also provide a direct comparison to traditional plastic bags, examining the initial outlay versus their long-term environmental value.
Understanding the economics of biodegradable bags is key to making informed choices for both consumers and businesses. Join us as we break down the cost considerations, explore the premium associated with sustainable materials, and shed light on their true worth in the evolving landscape of eco-conscious consumption.
Raw Material Costs
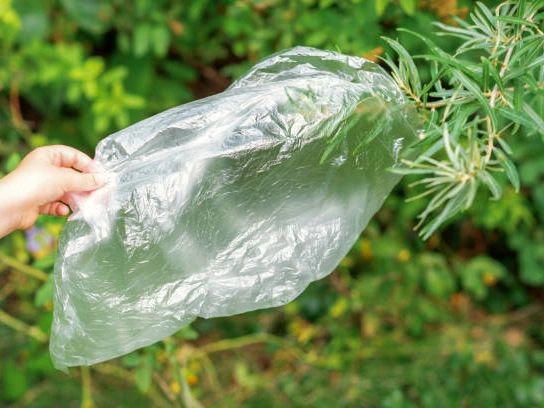
The raw materials used in making biodegradable bags are a significant determinant of the overall cost. One of the primary ingredients is often plant-based polymers such as polylactic acid (PLA), which is derived from renewable resources like corn starch or sugarcane. The cost of PLA can range from 2 to 4 per kilogram, depending on factors like the source of the raw material and the scale of production. For instance, large-scale producers who buy in bulk may enjoy lower per-unit costs.
Another common raw material is starch, which is more affordable, usually costing around 1 to 2 per kilogram. Starch-based biodegradable bags also often require the addition of plasticizers like glycerin to improve flexibility. Glycerin typically costs about 1.5 to 3 per liter.
Production Equipment and Facility Costs
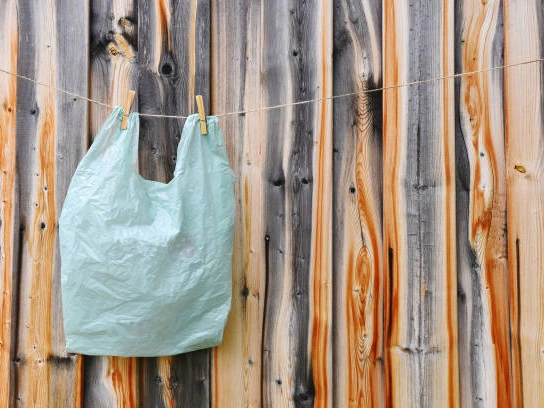
For small-scale home production, the equipment needed is relatively basic and inexpensive. A simple kitchen pot, a stirrer, and a basic mold can be used, with a total investment of perhaps \(50 to \)100. However, on an industrial scale, the costs skyrocket. Industrial-grade extruders, which are used to shape the biodegradable materials into bags, can cost anywhere from \(10,000 to \)100,000, depending on their capacity and sophistication.
Moreover, setting up a production facility involves costs such as rent, utilities, and maintenance. In a prime industrial location, monthly rent for a medium-sized production space can be \(5,000 to \)10,000, adding a substantial amount to the overall production cost.
Labor and Overhead Costs
Labor costs vary greatly depending on the region and the scale of production. In developing countries, where labor is relatively cheap, the cost of hiring workers to operate the machines, monitor the production process, and package the bags can be as low as \(5 to \)10 per hour per worker. In contrast, in developed countries, this figure can be \(20 to \)50 per hour.
Overhead costs include expenses like marketing, research and development, and quality control. Marketing is crucial for promoting biodegradable bags in a competitive market, and companies may spend a significant portion of their budget on advertising, trade shows, and online promotions.
How Much Do Biodegradable Bags Cost
Biodegradable bags typically cost more than traditional plastic bags, primarily due to the higher expense of their raw materials and the more complex manufacturing processes involved. While conventional plastic bags can cost as little as $0.01 per bag, biodegradable alternatives often range from $0.02 to $0.40 per bag at wholesale, depending on factors like:
- Type of Biodegradable Material: Different bioplastics (e.g., PLA, PBAT, PHA, corn starch-based) have varying material costs, with some being more expensive than others.
- Size and Thickness: Larger and thicker bags require more material, naturally increasing their cost.
- Order Volume: Bulk orders usually come with significant discounts, lowering the per-unit cost.
- Manufacturer and Certifications: Reputable manufacturers and bags with specific certifications (e.g., BPI compostable) may have a higher price point due to quality assurance and compliance.
How Much Does It Cost to Make a Biodegradable Bag
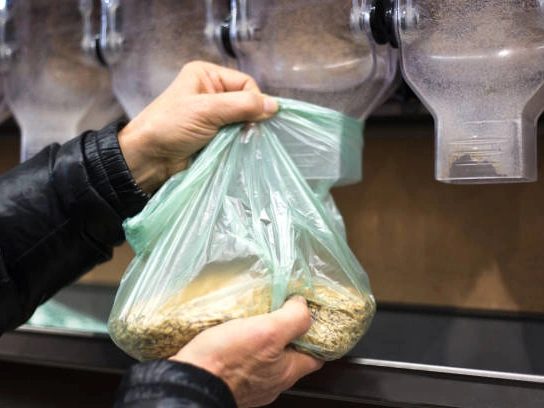
The cost of biodegradable bags is influenced by a multitude of factors. Generally, the market price of the most common biodegradable plastic hovers between 6 and 7 euros per kilo. However, this price can fluctuate significantly depending on the supplier, the wholesaler, the scale of the supply, and whether the packaging has any printing.
The cost of an individual bag is closely related to its weight. For instance, ultra-light bags designed for fruits and vegetables, which weigh only a few grams, may cost just a few euro cents. In contrast, thicker and heavier shopping bags will naturally have a higher cost.
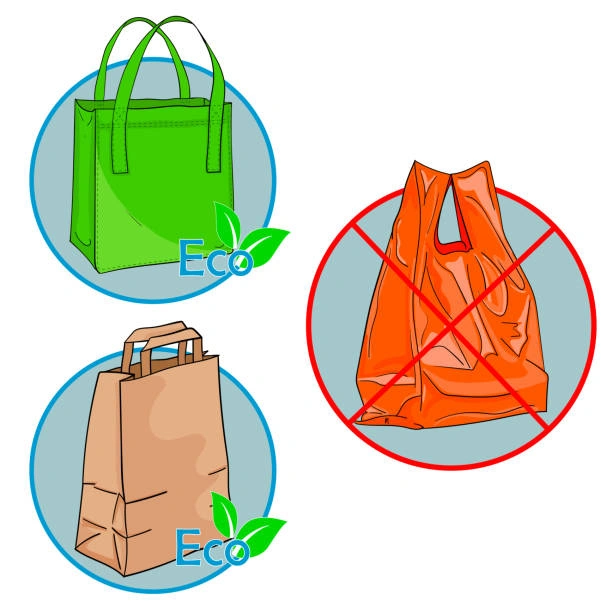
For small-scale retailers, excluding large distribution chains with different purchasing volumes, the cost of small bags, like those used in pharmacies, is typically between 1.5 and 2 cents per piece plus VAT. Larger shopping bags usually cost between 4 and 5 cents per piece plus VAT. Additionally, the cost of recyclable consumer-packaged goods (CPG) packaging depends on the materials chosen. Different materials bring distinct cost-effectiveness and performance, further complicating the cost calculation.
The Cost-Benefit Analysis
While the cost of making biodegradable bags may seem high compared to traditional plastic bags, it’s essential to consider the long-term benefits. Biodegradable bags reduce environmental pollution, which in turn reduces the costs associated with waste management and environmental cleanup. Additionally, as consumer demand for eco-friendly products grows, businesses that offer biodegradable bags may gain a competitive edge in the market, leading to increased sales and brand loyalty.
In conclusion, the cost of making a biodegradable bag is influenced by multiple factors, from raw materials to production scale and labor. However, with technological advancements and increasing economies of scale, the cost is expected to decrease in the future, making biodegradable bags an even more viable option for a sustainable future.
Biodegradable Plastic Bags Manufacturing Plant Cost
Setting up a biodegradable plastic bags manufacturing plant involves a significant initial investment, covering everything from machinery and raw materials to factory space and operational costs. The exact cost can vary widely depending on the scale of operation, the level of automation, and the specific type of biodegradable plastic being produced.
- Machinery: The core of the plant is the bag-making machinery, which can range from semi-automatic to fully automatic systems. Prices for these machines can be anywhere from approximately $3,000 to over $200,000, depending on capacity and features. A basic small-scale unit might start around $40,000.
- Raw Materials: Biodegradable plastics are typically made from renewable resources like corn starch, PLA (Polylactic Acid), PBAT (Polybutylene Adipate Terephthalate), or PHA (Polyhydroxyalkanoates). The cost of these raw materials is generally higher than petroleum-based plastics, often ranging from $1.00 to $3.00 per kilogram, though wholesale prices can vary.
- Factory Space and Infrastructure: You’ll need a suitable facility, typically 2,000-3,000 square feet for a small-scale unit, to house production, storage, and administrative areas. This involves potential rent or lease costs, along with significant investment in utilities like a reliable power supply (around 30-40 KW for a small unit).
- Operational Costs: Beyond initial setup, ongoing expenses include labor, maintenance, quality control, and obtaining necessary licenses and certifications (e.g., business registration, environmental permits). These recurring costs need to be factored into the overall financial planning for a sustainable business.
Conclusion
Although biodegradable bags cost more than traditional plastic bags, in the long run, they can reduce environmental pollution and reduce waste management costs. As demand grows and technology advances, costs are expected to decrease, and there is huge potential for future development.
At BN Pack, we specialize in custom organic food packaging solutions that meet your specific needs. From eco-friendly materials to unique designs and full-color printing, we offer a variety of options to help your products stand out. Our team will work closely with you to ensure your packaging meets your brand and regulatory requirements, providing solutions that enhance your product’s quality and market appeal. Contact us for more information.