Curious about how are plastic bags made? The process begins with polyethylene, which is melted and formed into thin sheets. These sheets are then shaped into bags using specialized machines. The bags are sealed to ensure durability and are ready for use in various industries. Understanding this process helps you appreciate the efficiency behind every bag.
Need plastic bags for your business? Quote your Plastic Bags from BN Pack today for quality and reliability.
Benefits of Plastic Bags
Here is a table of benefits of plastic bags:
Benefit | Description |
---|---|
Lightweight | Plastic bags are easy to carry and handle, reducing strain. Their compact size also makes them simple to store without taking up much space. |
Durable | Plastic bags are strong and resilient, able to hold heavy items without tearing. They keep your belongings secure during transport. |
Waterproof and Moisture-Resistant | They protect items from moisture, keeping products dry in rainy weather or preventing water damage to electronics and food. |
Versatility | Available in various sizes and shapes, plastic bags are adaptable for multiple uses, from grocery shopping to gift packing or organizing items. |
Cost-Effective | Plastic bags are affordable to produce, making them a budget-friendly option for businesses while maintaining high quality and reliability. |
What are Plastic Bags Made of?
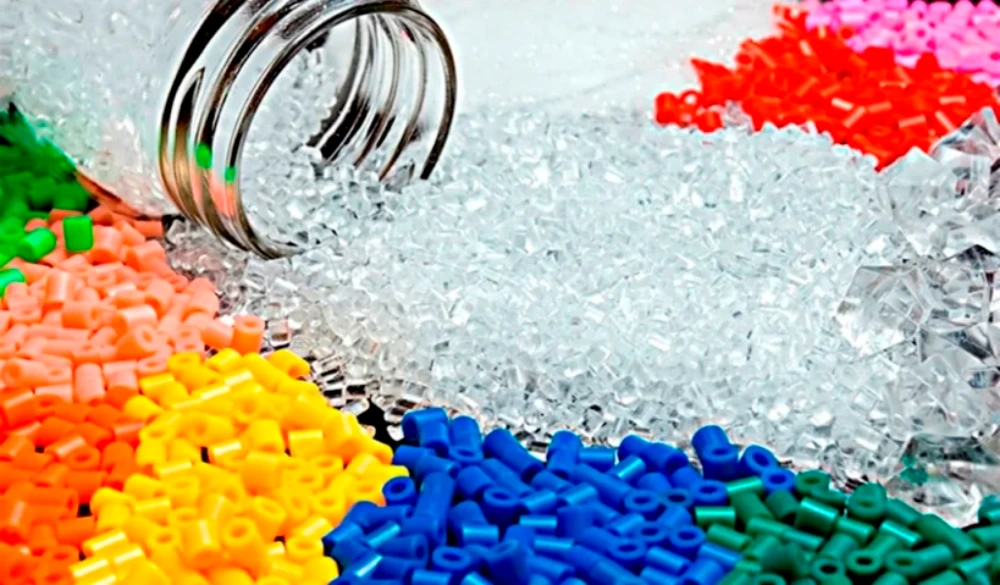
HDPE (High-Density Polyethylene)
Plastic bags made from HDPE are strong and stiff, offering excellent protection for products. This material is commonly used for grocery bags and is resistant to moisture. It’s also easy to recycle, making it a popular choice for businesses looking to reduce environmental impact. You’ll find it in many everyday bags.
LDPE (Low-Density Polyethylene)
LDPE plastic bags are flexible and lightweight, offering a soft, smooth feel. This material is often used for thin bags like bread bags or dry cleaning bags. LDPE bags are tear-resistant and provide excellent moisture protection. They’re not as rigid as HDPE but offer greater flexibility for a range of uses.
LLDPE (Linear Low-Density Polyethylene)
LLDPE combines the best features of both HDPE and LDPE. It’s flexible yet strong, often used for stretch wrap or shopping bags. These bags provide excellent puncture resistance, making them durable for heavier items. They’re also more stretchable, ensuring a tight fit for your goods without tearing.
MDPE (Medium-Density Polyethylene)
MDPE plastic bags strike a balance between flexibility and strength. They’re tougher than LDPE but more flexible than HDPE, often used for large bags like postal bags or industrial packaging. These bags offer moderate resistance to tearing and punctures, making them suitable for both retail and industrial use.
PP (Polypropylene)
Polypropylene is a durable and lightweight plastic often used for reusable shopping bags. It’s stronger than other plastics and can be woven into fabric-like materials. PP bags offer good chemical resistance and are highly resistant to fatigue, meaning they can last longer, even after frequent use. You’ll often find it in eco-friendly bags.
How Are Plastic Bags Made Step by Step?
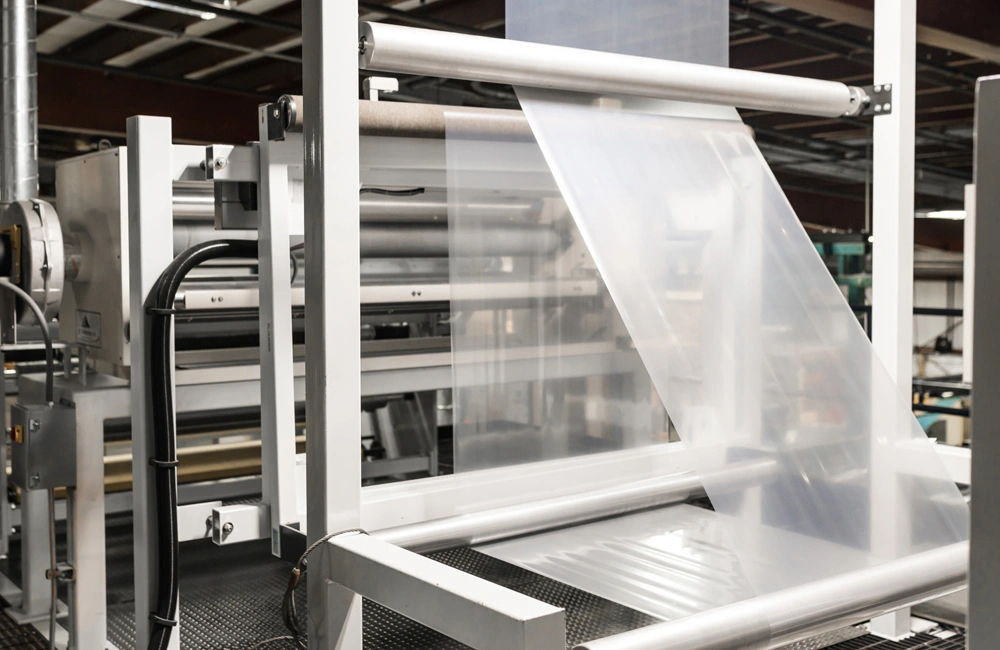
Step 1: Polymers to Resin Pellets
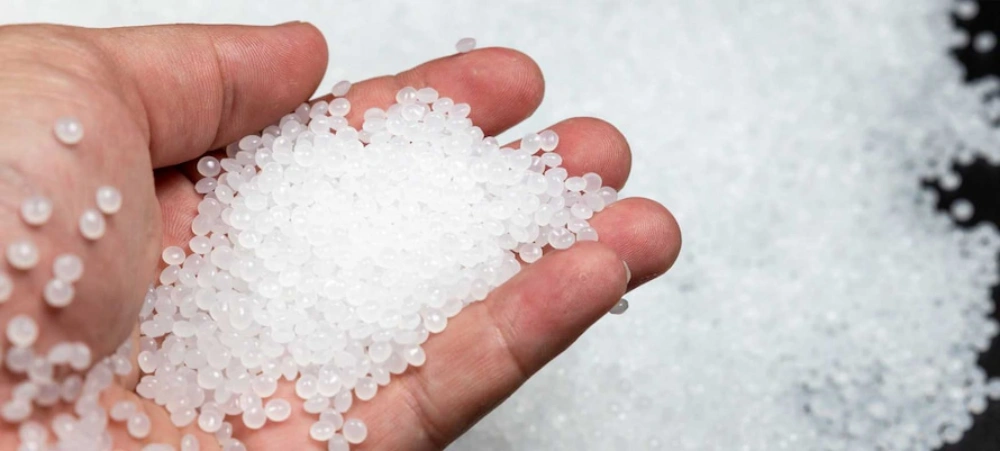
Plastic bags begin with polymers, which are large molecules made of repeated units. These polymers are turned into resin pellets by heating and compressing them. These pellets are the base material for plastic production. They are easy to handle and transport, ensuring efficiency in the manufacturing process.
Step 2: Extrusion: Crafting Plastic Film
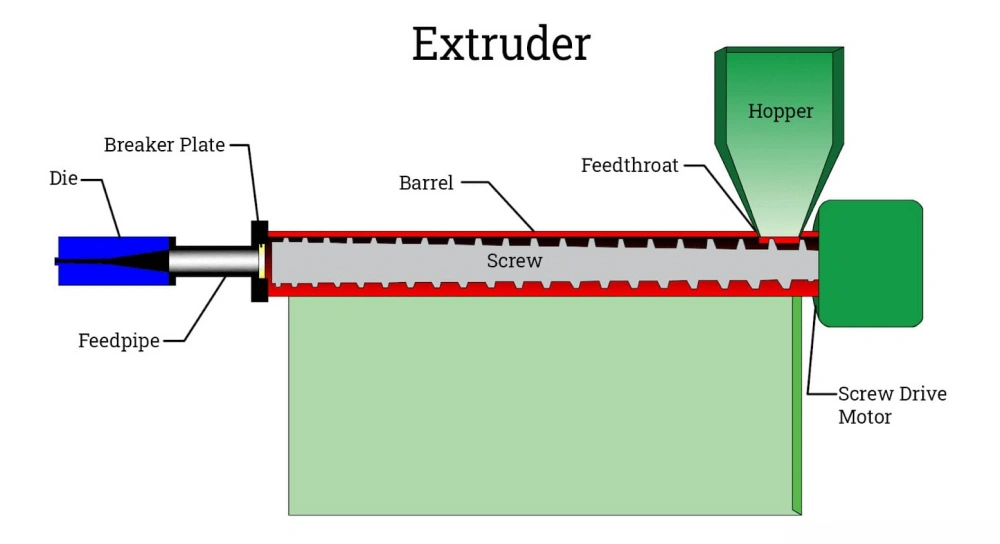
The resin pellets are fed into an extruder, where they are melted and formed into a thin plastic film. This film is shaped as it exits the extruder, and its thickness can be adjusted based on the type of plastic bag being made. The extrusion process allows for high volume production with consistent quality.
Step 3: Adding Color and Additives
After the plastic film is formed, colors and additives are added to enhance the plastic’s appearance and properties. The additives may include stabilizers, anti-slip agents, or UV inhibitors. These additives improve the functionality of the bags, whether for durability, appearance, or protection from environmental factors.
Step 4: Cooling and Setting the Film
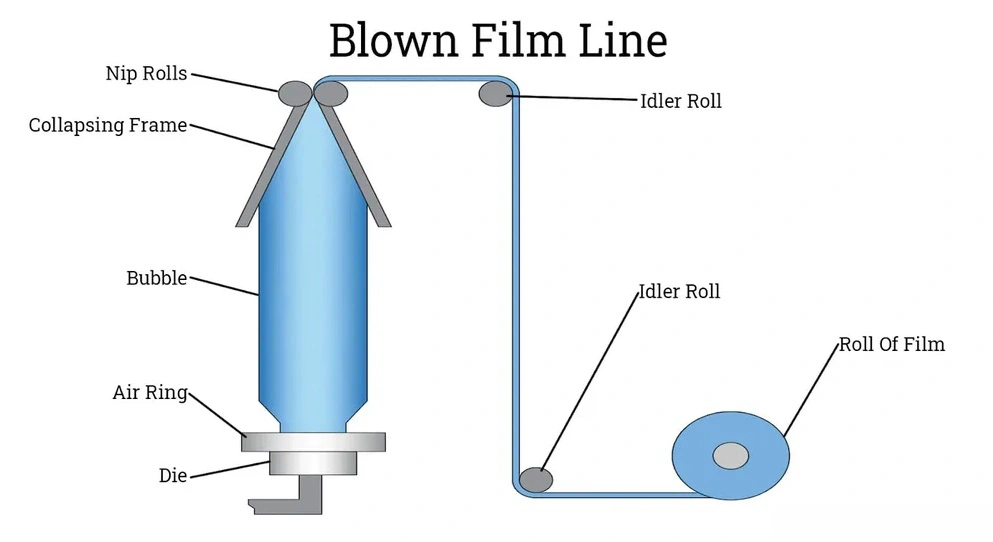
The heated plastic film is cooled rapidly to set its shape and solidify it. This step is crucial to ensure the plastic maintains its strength and flexibility. As the film cools, it’s stretched slightly to improve its strength, giving it the durability needed to carry various items without tearing.
Step 5: Quality Control: Testing Plastic
During production, the plastic is regularly tested for thickness, strength, and other desired properties. This ensures each bag meets industry standards. If any issues arise, the process is adjusted to maintain quality. Regular quality control helps avoid defects that could compromise the bag’s usability.
Step 6: Packaging for Distribution
Once the plastic film is properly set and tested, the material is cut into the desired bag sizes. These bags are then folded, stacked, and packed into bundles for easy shipping. The packaging process is efficient, ensuring that the bags are ready for quick distribution to retailers or manufacturers.
Step 7: Recycling or Disposal of Plastic
Plastic bag production generates waste, such as leftover resin pellets or plastic trimmings. This waste is often recycled, reducing environmental impact. Some factories may reuse this scrap material in the production of other bags, contributing to a more sustainable manufacturing process.
Step 8: Final Product Ready for Use
After packaging, the plastic bags are ready for distribution and use. They can be found in stores, used for shopping, or employed for industrial purposes. With their efficient production process, plastic bags remain a widely used and versatile product in daily life and commercial applications.
How Are Biodegradable Plastic Bags Made?
Biodegradable plastic bags are made from renewable plant-based materials like corn starch or vegetable oils, instead of traditional petroleum-based plastics. The process starts by creating biopolymers, which are mixed and processed into pellets. These pellets are then melted and extruded into thin films.
Additives are included to help the bags degrade over time. The film is cooled, tested for quality, and then cut into bags. Finally, the bags are packaged and distributed for use, offering an eco-friendly alternative to traditional plastic bags.
How Are Single Use Plastic Bags Made?
Single-use plastic bags are made from polyethylene, a petroleum-based material. The polyethylene pellets are melted and fed into an extruder, where they are formed into thin sheets. These sheets are then cooled and stretched to achieve the right thickness and flexibility.
The plastic is cut into bag shapes and sealed with heat to form the edges. Finally, the bags are tested for quality and packaged for distribution, ready for use in stores.
How Are Plastic Bags Made Chemically?
Plastic bags are made chemically from polymers, which are long chains of molecules. The process starts with the extraction of raw materials like petroleum or natural gas. These materials are refined into monomers, such as ethylene.
The monomers are polymerized, turning them into polyethylene, the plastic used for bags. The polyethylene is then melted, shaped into films, and cooled. After cooling, the plastic is cut into bags, ready for packaging and distribution.
How Are Plastic Bags Made From Oil?
Plastic bags are made from oil, starting with extracting crude oil. The oil is refined to produce ethylene, a key building block for plastic. The ethylene is then polymerized, meaning it’s chemically bonded into long chains to form polyethylene, the plastic used for bags. The polyethylene is melted and formed into thin films. These films are cooled, cut into bags, and tested for quality. Finally, the bags are packaged and ready for use.
Why Choose Bn Pack Plastic Bags?
Choose BN Pack plastic bags for their durability, strength, and versatility. Our bags are made from high-quality materials that ensure reliability for various uses. They are lightweight, cost-effective, and provide excellent protection for your products.
With customizable sizes and styles, BN Pack plastic bags meet your unique packaging needs. Plus, they are eco-friendly, offering a sustainable solution without compromising on performance.
Conclusion
Now you know how plastic bags are made, from raw materials to the final product. The process involves melting, molding, and testing to ensure quality. Whether you need plastic bags for retail, food packaging, or industrial use, understanding the manufacturing process helps you make an informed choice.
Ready to get high-quality plastic bags for your business? Quote your plastic bags today from BN Pack and experience reliable, durable packaging solutions.
FAQ
Where Are Plastic Bags Made?
Plastic bags are made in factories around the world, often located near oil refineries or plastic production plants. These factories use large machines to process raw materials into plastic bags.
How Are Plastic Grocery Bags Made?
Plastic grocery bags are made by melting polyethylene pellets and extruding them into thin sheets. These sheets are cut and sealed to form bags, which are tested for strength and quality.
How Are Plastic Shopping Bags Made?
Plastic shopping bags are made by heating polyethylene, then extruding it into a thin film. The film is cooled, cut into the right size, and sealed. After quality checks, they are ready for use in stores.
How Many Plastic Bags Are Made a Year?
Over 500 billion plastic bags are made each year worldwide. This includes bags for groceries, shopping, and various packaging needs.
How Many Plastic Bags Are Made Each Day?
Every day, factories produce millions of plastic bags. This number varies based on demand but typically reaches hundreds of millions globally.
What Are the Raw Materials for Plastic Bags?
The main raw materials for plastic bags are petroleum-based products like ethylene and propylene. These are refined into plastic polymers like polyethylene.
Are Plastic Bags Easy to Produce?
Yes, plastic bags are relatively easy to produce. The process involves simple steps like melting, shaping, and sealing plastic, making it efficient for large-scale production.
Is it Expensive to Make Plastic Bags?
No, making plastic bags is not very expensive. The materials are inexpensive, and the manufacturing process is highly automated, which keeps production costs low.